SD6 servo drives with safety functions
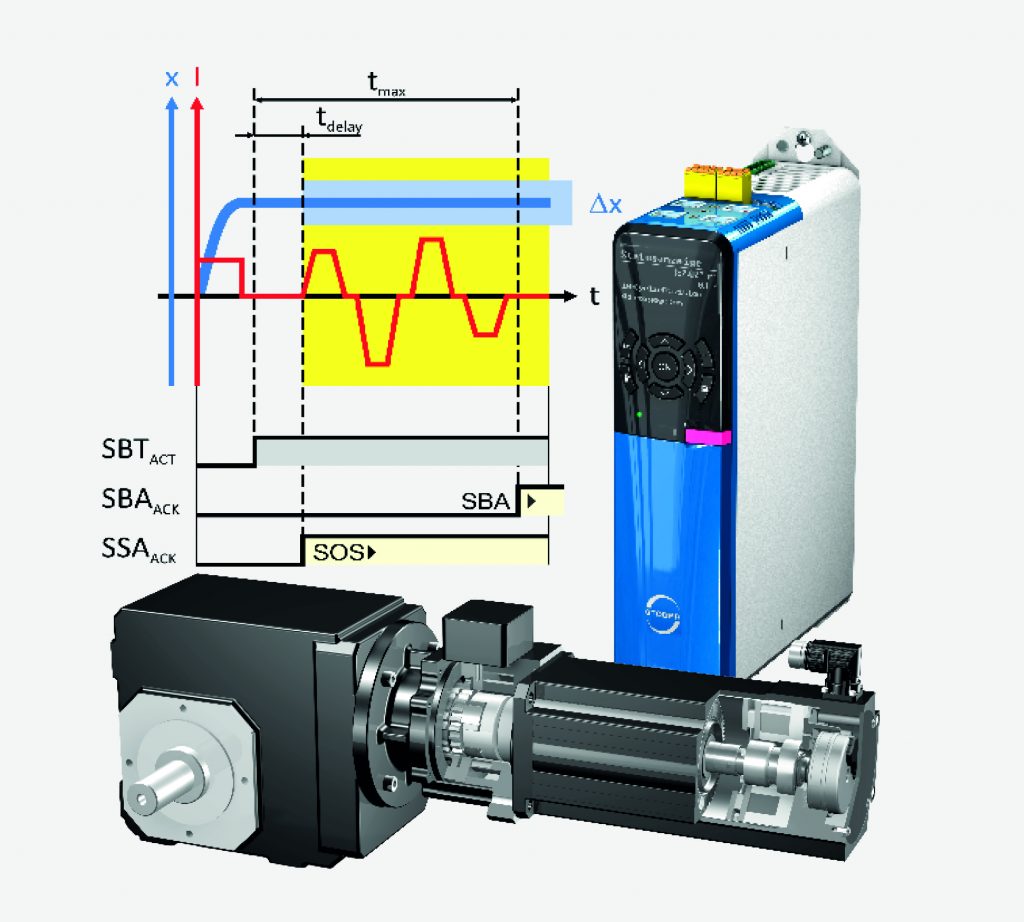
SD6 servo drives are motion controllers for electric synchronous (servo) and asynchronous (induction) motors, equipped with the SE6 safety module, a product jointly developed by STOBER and Pilz GmbH & Co. KG. Thanks to its high computing power, the SD6 recalculates the position, speed, and torque control of the servo axis every 62.5 μs. The rated current ranges from 2.3 to 85.0 A.
Features of SD6 Servo Drives:
-
Integrated 32-bit dual-core processor.
-
Built-in functions for positioning, synchronization, flying saw, electronic gearbox, speed and torque control.
-
High control dynamics for position, torque, and speed, calculated in a 62.5-microsecond (16kHz) cycle.
-
Maximum positioning resolution of 33 million pulses per revolution of the servo motor.
-
Operates in a closed-loop control system.
-
Output frequency control range: 0 – 700 Hz.
-
Safety technology: Safe Torque Off (STO) as standard.
-
Operates in CiA 402 mode.
-
Communication via ProfiNET IO, EtherCAT, or CANopen.
-
SD6 supports ProfiNET IO-RT communication.
-
Internal IGB system bus for parameterization, programming, and synchronization of multi-axis drive applications.
-
Regenerative energy utilization in multi-axis applications via DC-link bus.
-
Integrated brake control with 24 V(DC) supply.
-
Optional digital and analog inputs and outputs.
-
Brake management with cyclic brake test and brake-in functions.
-
Free DriveControlSuite software for fast commissioning, programming, and diagnostics.
-
Fully programmable according to PLCopen standards.
-
Paramodule – removable memory card with application parameters.
-
Automatic motor parameterization via the electronic nameplate of the servomotor.
-
Independent power supply for power and control sections.
-
Integrated line filter.
-
Complies with the following directives: Machinery, Low Voltage, and EMC.
-
IP20 protection class – designed for installation in an electrical cabinet.
-
Galvanized steel sheet housing.
-
Certifications: CE, UL (UL508C and UL840), cUL (CSA-UL).
SD6 Servo Drives – Encoder Compatibility:
-
Absolute EnDat® 2.1/2.2 Multiturn/Singleturn
-
Absolute EnDat® 3.0 – single-cable OCS
-
Absolute SSI
-
Incremental
-
Resolvers
-
Optional: EnDat® 2.1 sin/cos
SD6 Servo Drives – Communication Capabilities:
-
EtherCAT®
-
PROFINET®
-
CANopen®
Extended Safety Technology in SD6/SE6 Servo Drives:
SD6 servo drives with the SE6 safety module offer innovative, encoder-independent safety functions and safe management of up to two brakes.
The comprehensive safety functions meet the requirements of the EN 61800-5-2 standard and are certified in accordance with SIL 3, PL e (Category 4).
In addition to the Safe Torque Off (STO) function, advanced safety functions compliant with EN 61800-5-2 are available, including extended stop and monitoring functions.
Advanced Safety Functions (SIL 3, PL e, Category 4):
-
STO – Safe Torque Off
-
SS1 – Safe Stop 1
-
SS2 – Safe Stop 2
-
SLS – Safely Limited Speed
-
SBC – Safe Brake Control
-
SBT – Safe Brake Test
-
SDI – Safe Direction
-
SLI – Safely Limited Position
Extended Stop and Motion Functions in SD6 Servo Drives with SE6 Module:
-
SS1, SS2, SDI, SLI, SLS, SOS (Safe Operating Stop), SSR (Safe Speed Range), SLP (Safe Limited Path)
-
Apart from SS1, ten additional safety functions can be parameterized and flexibly assigned.
Safe Brake Management in SD6/SE6 Servo Drives:
-
Safe control of up to two brakes (SBC)
-
Testing and required monitoring of the brake test cycle (SBT)
-
Compliant with DGUV safety requirements for vertically loaded, gravity-affected axes
Safe Monitoring in SD6/SE6 Servo Drives:
-
SDI, SLI, SLS, SOS, SSR, and SLP also available as monitoring functions
Controlled Stopping in SD6/SE6 Servo Drives:
-
Application-specific stopping of drives in case of limit value exceedance or emergency stop
Optional:
-
Direct control or safe monitoring of the braking ramp
Are your drive movements safe?
The SE6 safety module from STOBER offers safety functions for applications requiring functional safety up to SIL 3, PL e (Cat. 4) in accordance with DIN EN 61800-5-2 and DIN EN ISO 13849-1.
In addition to the basic safety function Safe Torque Off (STO), SE6 provides extended safety features including Safe Stop 1 (SS1), Safe Stop 2 (SS2), Safely Limited Speed (SLS), Safe Brake Control (SBC), Safe Direction (SDI), and Safely Limited Position (SLI). These normative safety functions are complemented by practical additions like Safe Brake Test (SBT).
Are your vertical drive axes safe?
Safe brake management goes beyond just safe control!
The German Social Accident Insurance Association (DGUV) defines safety requirements for vertically loaded axes influenced by gravity.
With the optional SE6 safety module, the SD6 meets DGUV safety requirements for gravity-loaded vertical axes. Safe brake management supports secure control of up to two brakes, along with testing and necessary test cycle monitoring.
Are your safety functions flexible enough?
Choose drive components from the entire STOBER product range for safety-related applications.
Multi-vendor interfaces allow freedom in selecting motors and encoders (synchronous servo motors, asynchronous motors, linear motors, hollow-shaft servo motors, etc.). You can continue using your current motor, encoder, and cable — or select what best fits your needs.
Freely assignable functionality: Beyond the standard SS1 function, 10 additional safety functions can be configured and flexibly assigned to safe inputs and outputs.
Simple service concept
In case of service, simply replace, verify, and test the Paramodule – that’s all. No special skills required!
Safe monitoring
Send a safe signal instead of forcing a shutdown. This enables flexible safety control solutions, especially in complex systems.
Controlled shutdown
Benefit from short response times, reduced safety distances, and faster recovery. The SE6 enables application-specific stopping of drives when thresholds are exceeded or during an emergency stop. You have the option of directly controlling the braking ramp or safely monitoring it.
Do you need to sacrifice performance or availability?
Not at all — the STOBER SE6 safety module offers a simple, streamlined solution that saves space, time, and money!
-
Use existing hardware: No need for special motors, encoders, cables, or stuck/speed detection switches.
-
Respond quickly: Worst-case reaction time under 10 ms, enabling rapid stopping and minimized safety distances.
-
Avoid unintended triggering: Monitor your thresholds based on position and filter out specific noise pulses using tolerance windows.
-
Continuous monitoring: Controller-independent monitoring reduces the number of safe I/Os required on the main safety controller.
-
Quick and easy commissioning: The DriveControlSuite software guides users through the selection and configuration of safety functions with intuitive wizards and provides support for motion monitoring and diagnostics.
Instructions
443186_09_IBAL_SD6_pl.pdf – Stober SD6 servo drive user manual in Polish
442796_03_HB_SE6_en.pdf – Operating instructions for the SE6 safety module in SD6 servo drive in English